Polyend Interview
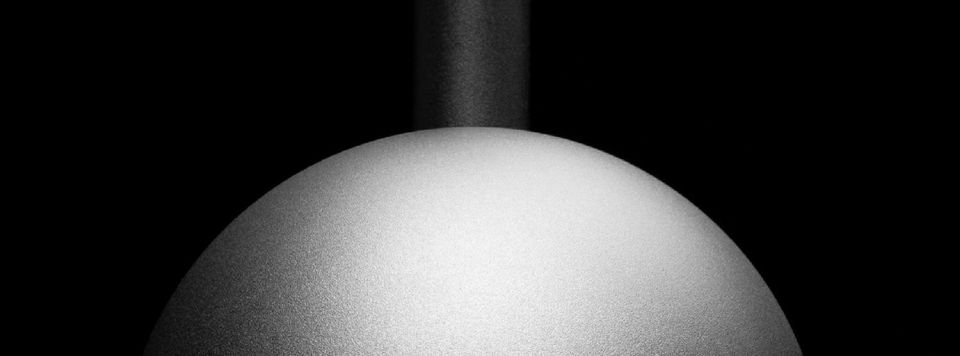
Creating a hardware instrument requires a voluminous quantity of courage. The sheer number of steps involved, layers of complexity, potential pitfalls and distractions are so great that it's really quite incredible that any musical hardware is created. Couple that reality with the difficulty of competing with large corporations that carry emotional cachet such as Roland or Korg, and it can seem like a retelling of David and Goliath, or Roland and Polyend, with one wielding a TB-303 and the other a SEQ. Yet, thankfully the arena is large enough that we electronic musicians are privvy to a seemingly endless list of machines to utilize.
There are many attempts to clone, repackage and capitalize on the popularity of electronic music machines from the 80's. These boxes are safe, easily classified, and only marginally different from their ancestors. Over time, the growing abundance of such hardware normalizes what was at one time a bastardization. The TB-303 was meant to be a bassline accompaniment for guitarists, not usher in Acid music.
Indeed, the prevalence of almost generic dance music gear can seem stifling or at least underwhelming. In a general sense, dance music is now a very safe place. However, there would be no dance music without Kraftwerk boldly going wherever the fuck they decided to go in the 70's. And forget about Acid or all its incalculable offspring if Dj Pierre hadn't used the wrong tool for the right job.
It is certainly noteworthy that most of us humans tend towards the more familiar sounds. We reward greatly those artists who teeter across the balance between the safe and the uncomfortable in a way that is palatable yet dangerous and exciting. In a way that is radically new to previous eras, the instruments, controllers, or other gear bearing buttons, can play just as profound a role as the sound itself. Marshall McLuhan already told us so.
To that end, it is important to celebrate the makers, not content with simple, incremental updates but large-sweeping waves of unmissable change. Polyend is one such company, a relatively spritely team of eight specializing in the dizzying breadth of fields required to pull off not just a profitable or intuitive product, but an excitingly innovative one.
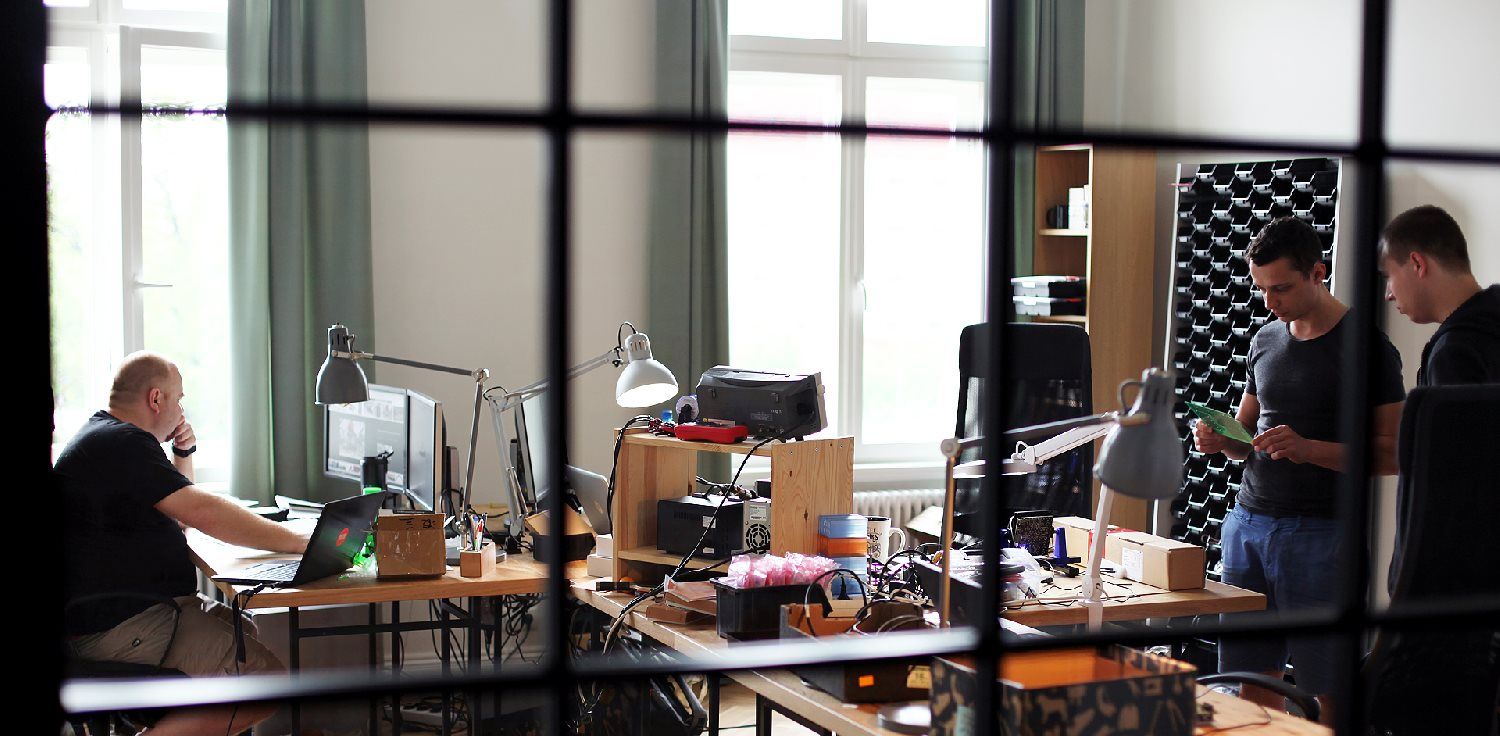
Started in 2015, Polyend made their feature debut with the brave, mallet-sized Perc Pro for midi-controlled percussion and the wild, beastly-but-lovable, 32-step SEQ sequencer. Just as you'd be happy to have found a thrilling new music producer whose work you greatly enjoy, Polyend is a company whose products you should happily squirrel away money to buy and anticipate.
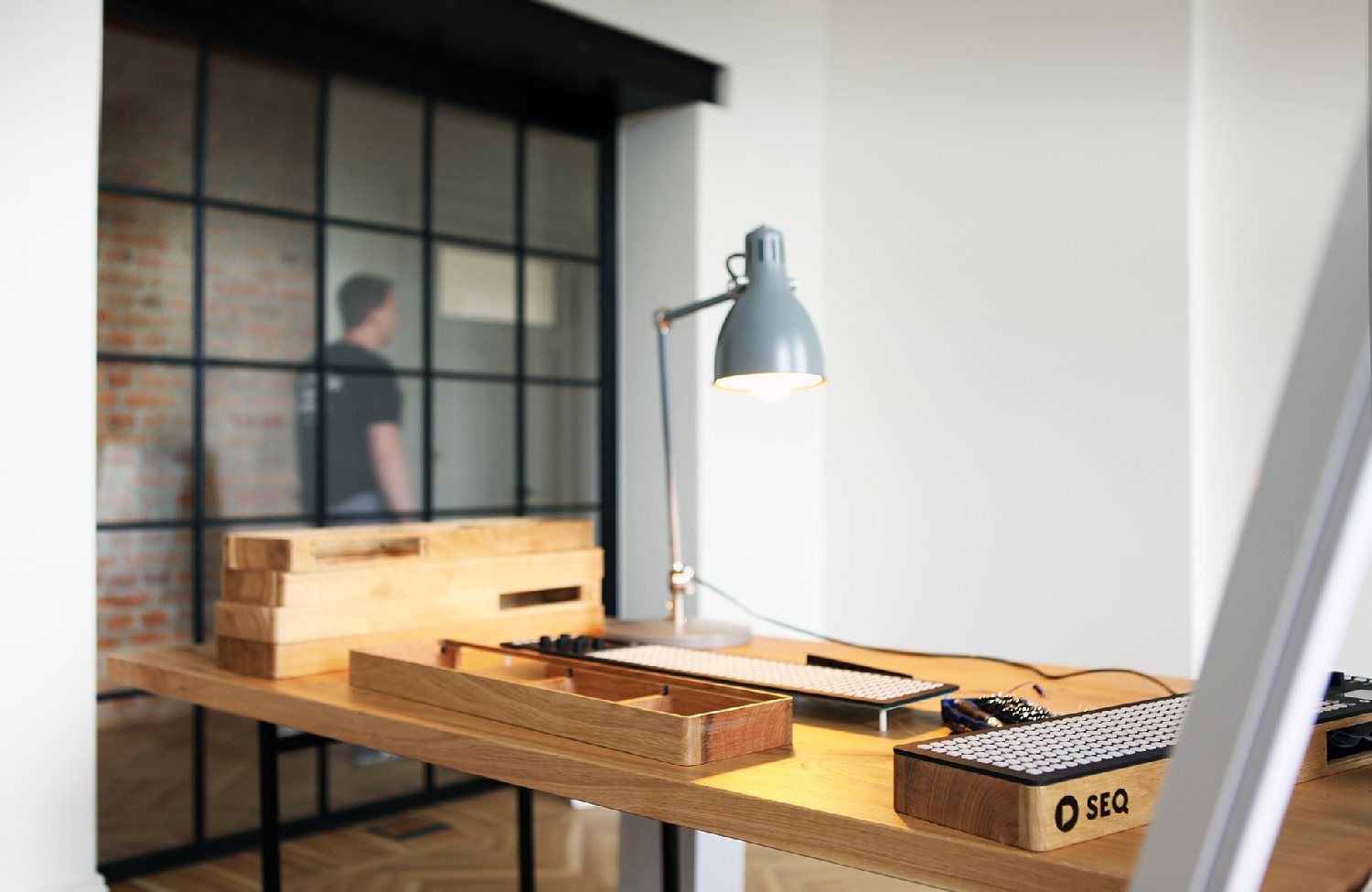
Do you plan things out methodically in advance or do you just experiment and see what happens?
We plan as much as we can. Running a business and few simultaneous projects require us to look at them in advance from many angles: PCB design, software, industrial design, supply chain, manufacturing, assembly, marketing, etc. There are too many parties involved in each project to let it run freely.
Also, we have too many ideas, so we need to address them methodically. We have developed a platform that enables us to produce prototypes fast and validate if an idea is worth developing further. So many ideas, so little time.
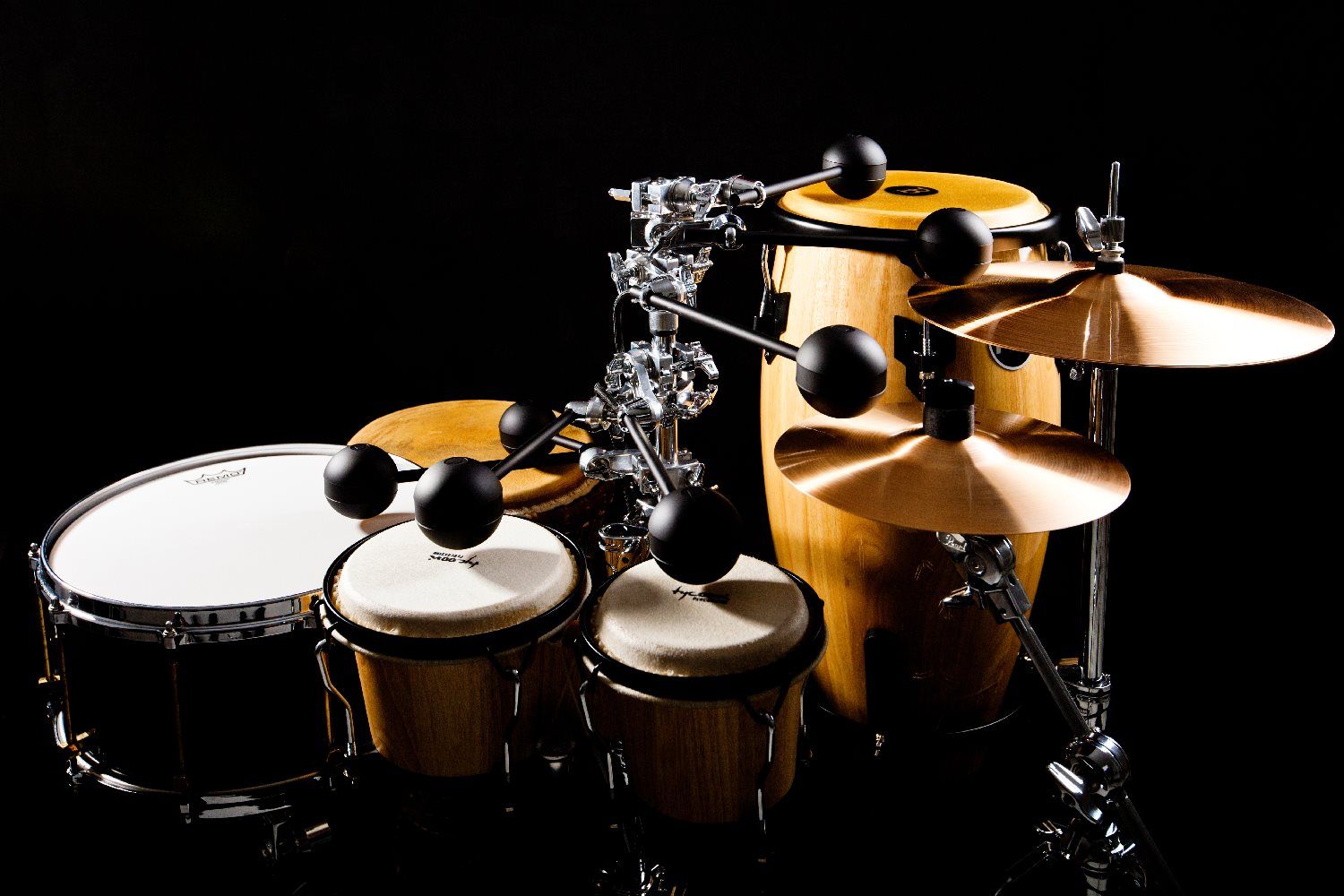
How do you stay focused?
We are a small and very dedicated team, so it's not that hard to stay focused on the job within the group. We make 10-15 minutes stand-up meetings each day to make sure we are all heading the same direction. Also, we use few tools that help us like: Slack to communicate, Dapulse to keep track of tasks and time, Google Sheets to keep track of the expenses.
The hardest part is to stay focused on the product features. It's been our mantra from the very beginning: Polyend makes devices that inspire. We look at many other devices and instruments and think why one is more inspiring than other. We figured out that acoustic instruments are the best in that field. They are not packed with complicated features, they are extremely well manufactured, they are always on and not much manual reading is needed to start playing it. We try to follow the same path with our electronic devices. It sometimes means getting rid of instead of adding features or looking for expensive materials rather than lowering the production costs. Also related to that is user experience which is critical to us. We won't add a feature unless it's obvious or easy to use/remember.
What relevant training, if any, do you have?
I graduated with a degree in IT, and I studied music production and marketing for a while. In my previous job, I was responsible for marketing and project management. But the most important has always been my passion to music tech. Of course with such a skillset, I wouldn't be able to make it on my own. So I found the perfect team members. Some are old friends, some are new friends, but each one of us has loads of experience in the different field (PCB design, software, industrial design, supply chain, manufacturing, assembly, marketing).
What technologies, techniques or trends are you curious about incorporating in the future?
We love MIDI and polyphony so for sure we will take a closer look at MPE and try to incorporate it into some form of new controller.
Also, we think it's still a cool concept to be able to control real instrument with computing power, so we'll continue with the technology we started developing with Perc Pro and pass it on to next instrument.
Of course, we are fascinated with Eurorack modules, and we have loads of ideas there as well.
What music have you and the team been listening to lately?
We love the moment when we receive an order, and it occurs to us that the one who ordered is an artist we all know. Suddenly all the office is filled with his music. So recently it was Alexis Taylor and Hotchip, Future Sound of London, Ricardo Villalobos. Apart from "the orderers" we've been recently listening to new albums from Fleet Foxes, Actress, Slowdive, Biosphere... probably too many to list it all.
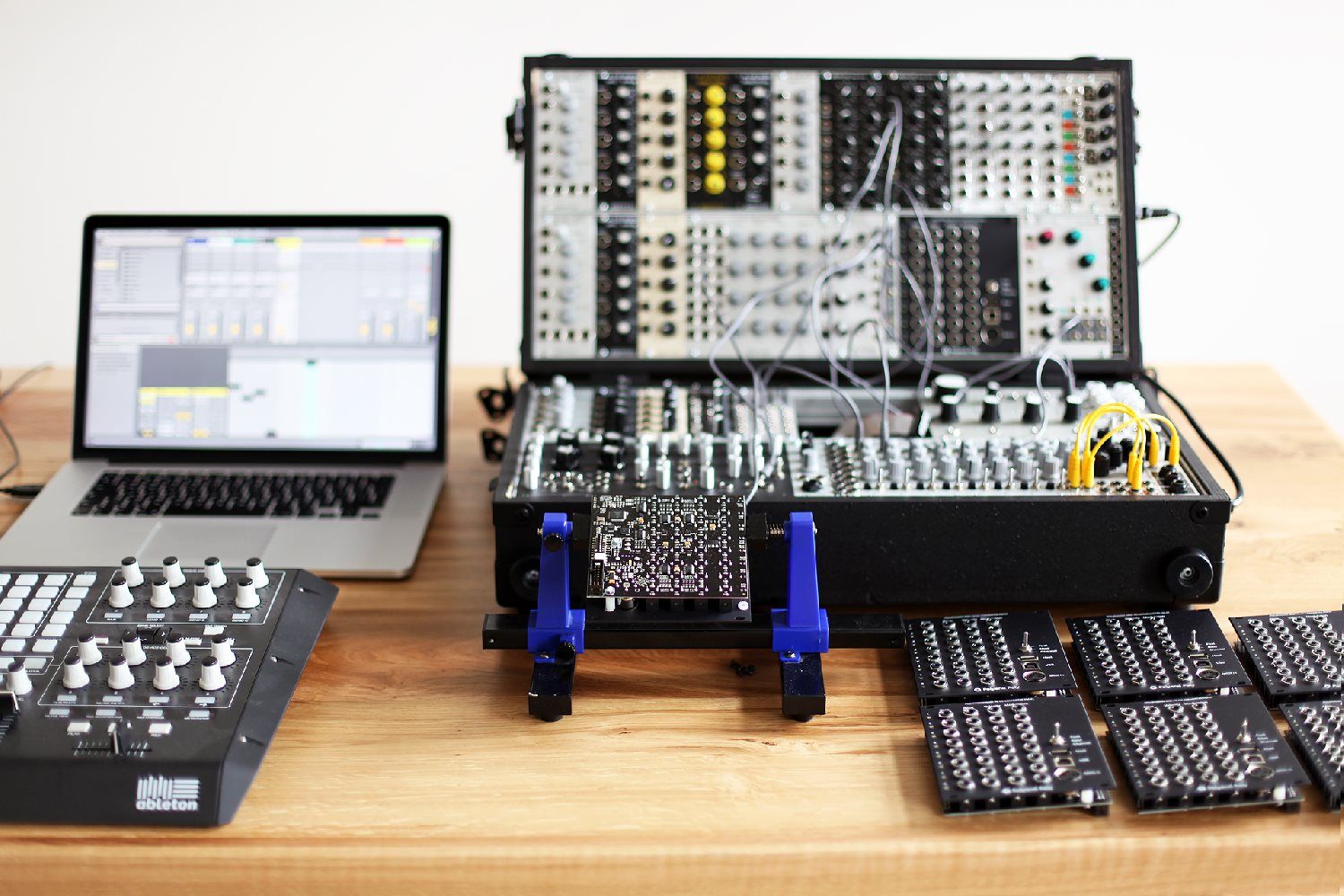
What are some of the biggest challenges you've faced, technically (process, algorithms, etc), financially, etc?
Running a hardware producing company means having to face different challenges each day. Of course, they change depending on the company's stage. So in the very beginning, we needed to find reliable manufacturing partners for example. We build our products with a lot of different materials like aluminum, wood, silicone and we do it with great care. It helps a lot when people you work with understand and can meet your quality standards. Now, with the rise of demand, the hurdle is the speed of manufacturing and assembly. As we'll figure it out, something else will pop up. This is the fun of running such a business.
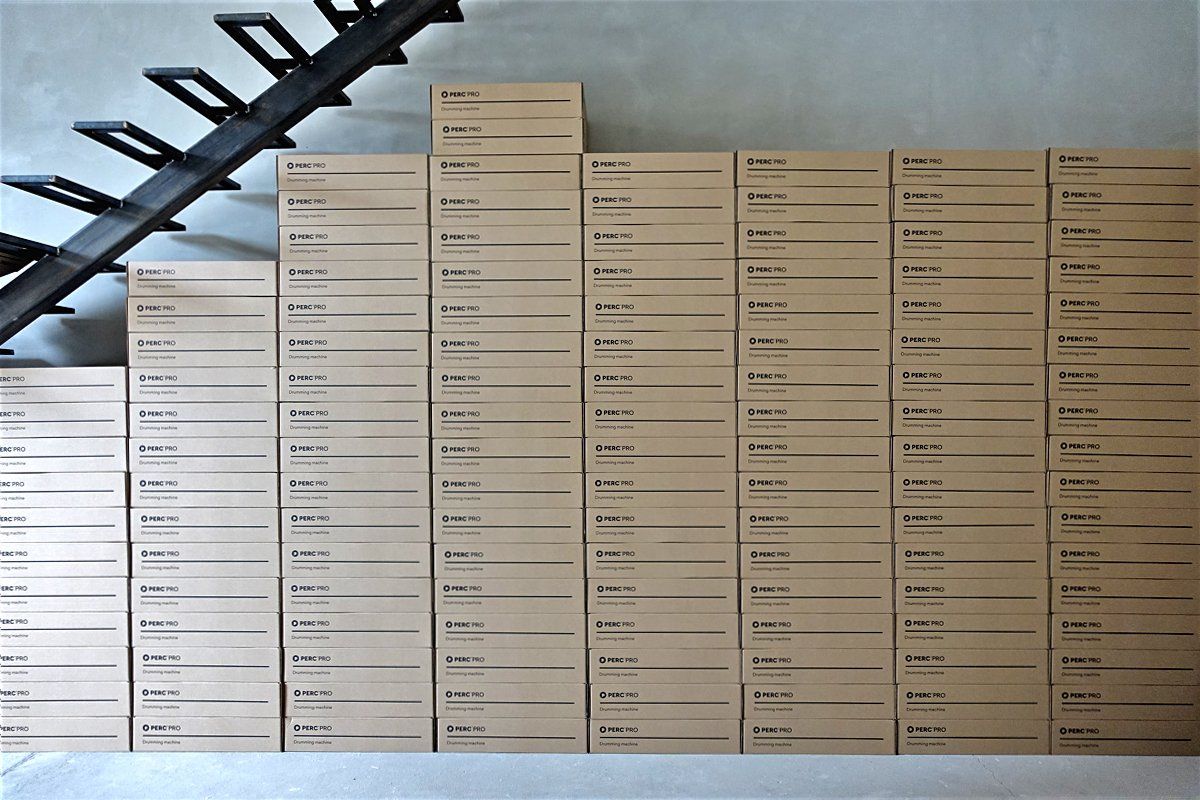
What recommendations do you have for others looking to get into production?
I'd say, love what you do, believe in it, and be very patient. We had to put a lot of effort to introduce our first device into the market. It took us more than a year to see first revenue from it. There is still plenty to do, but we already feel it's getting easier with next developments. So I'd also suggest having a plan for more than just one project and let one development benefit from the other.
Among the broad spectrum of modular synth makers, what are some modules you are really into?
Poly converted my modular into a polyphonic synth, so I've been playing with different sets of VCOs and filters recently. I like those modules that have the same principals as our devices - don't make me read the manual (unless I want to get really deep), have a clear interface and inspire me. I've been playing recently with Mutable Instruments Rings a lot. I also like the style of Qu-bit Electronix. I use their Chord, Wave and Chance.
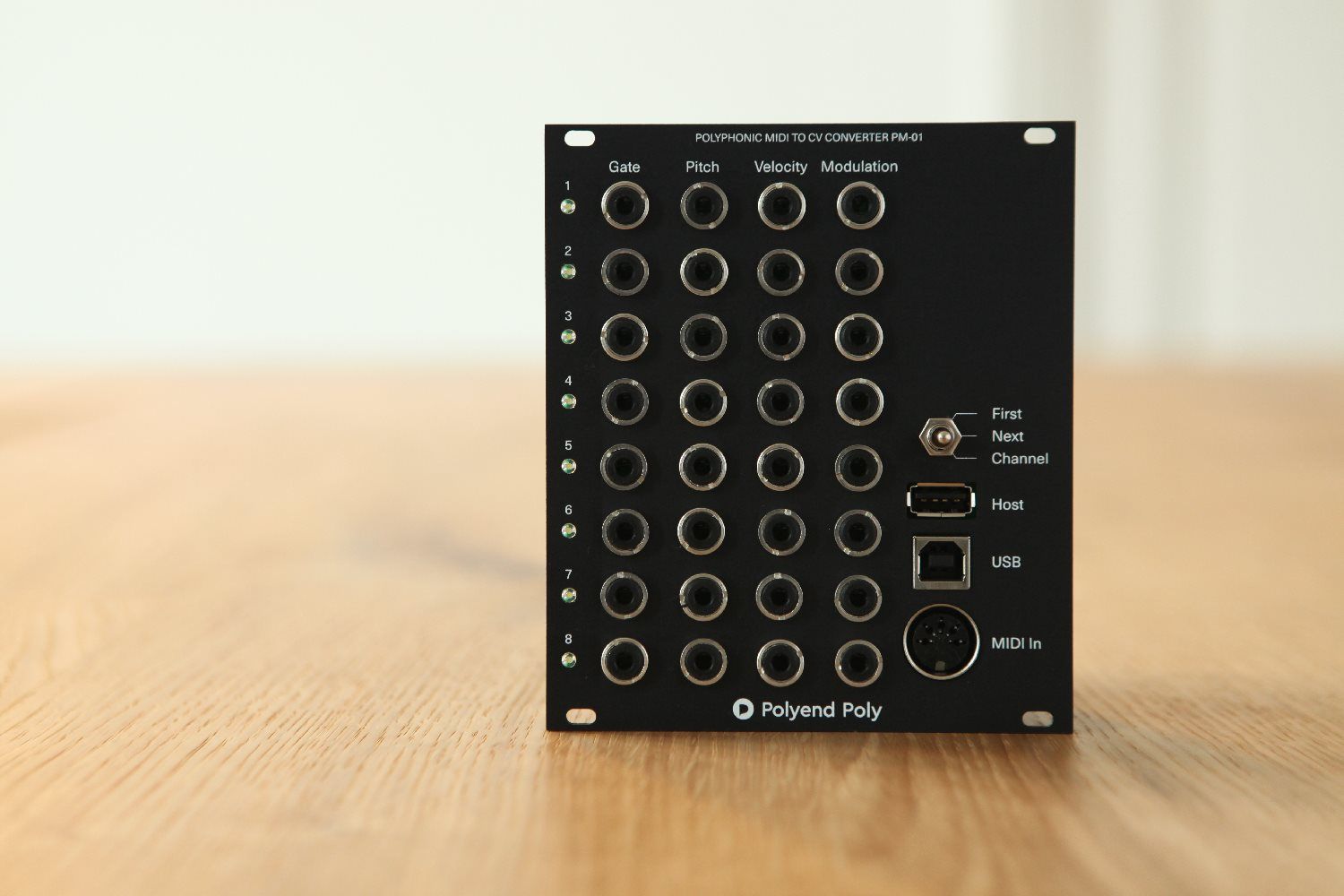
Any hint of info about unreleased upcoming projects?
As mentioned we are working on an MPE controller and next implementation of our Perc Pro technology. We a are also prototyping some rather unique Eurorack module, but I can't disclose more information about it yet.
Member discussion